Technical Parameters
Voltage: | AC 380V 3 Phase 50/60 HZ 15 kw |
Filling Principle: | Volumetric |
Fill Range: | Min. 50 ml, Max. 750 ml |
Production Speed: | 60 pcs./min (May vary according to tube size and filling volume.) |
Area of Use
This machine is widely used for filling cosmetic, chemical and food products.
It can be integrated with inlet and outlet labeling etc. machines.
- Advanced easy-to-use PLC control unit
- 316 quality stainless steel filling tank with precise level control
- Precise volumetric filling unit with 8 nozzles controlled by servo motor
- Separate capping for flat and round bottles
- Ability to control input, output and all operations thanks to sensors
- Easy product changeover, wide range of bottles and products to fill
- Ability to fill various sector products such as shampoo, liquid detergents, cream, vegetable oils, etc.
Our 8-head servo volumetric liquid filling machine is designed for large-scale industrial production. It maximizes production efficiency by accelerating high volume filling processes in the cosmetic, chemical, food and pharmaceutical industries. Thanks to its servo motor controlled filling system, it ensures precision and consistency, guaranteeing equal filling of each bottle.
Advanced Servo Volumetric Filling Technology
Our machine has the ability to fill more than one bottle at the same time with 8 different filling heads. Servo motor assisted filling systems provide precise flow control depending on product viscosity. It offers a fully automated operation from bottle inlet to bottle outlet, ensuring highly efficient production processes.
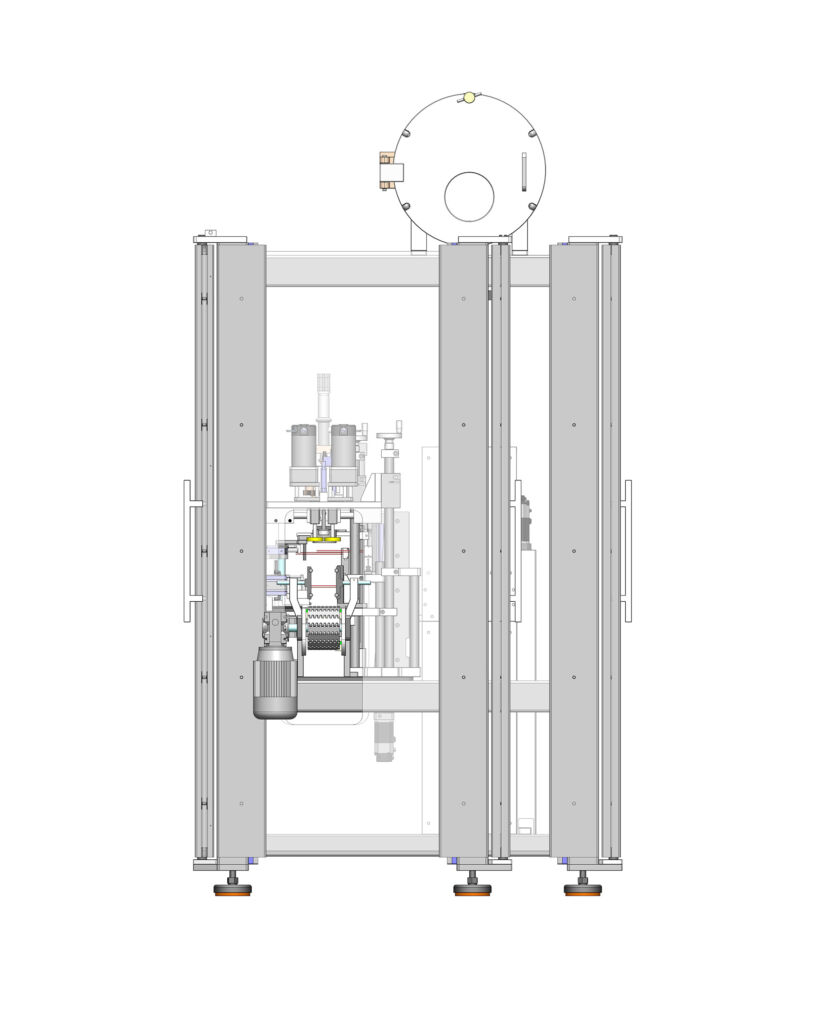
Precise Sensor Controlled Operation
Thanks to automatic sensor systems, it is checked whether the bottles are in the correct position during the filling process. Missing or incorrectly positioned bottles are automatically detected and incorrect filling is prevented. This feature minimizes the waste rate in production lines and ensures continuous quality control.
- 8-head servo volumetric filling system: Multiple filling capacity at the same time.
- Sensor-assisted fault detection: Prevents incomplete or incorrect filling.
- System compatible with different filling volumes.
- Fully integrated production line: Filling, capping and conveying in one system.
